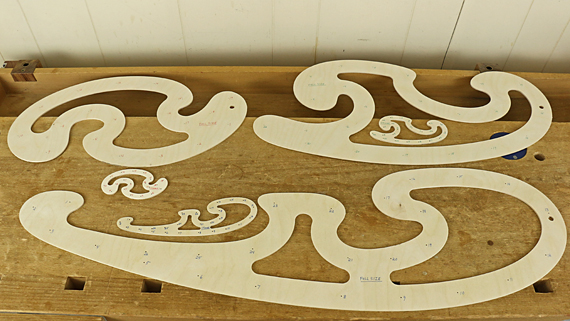
These useful tools from Veritas are paired sets of French curves. The small and large members of each pair have the same curve pattern in a 1:4 ratio.
This allows you to draft on paper at the commonly used scale of 3 inches = 1 foot using the small curve of the pair and then transfer the drawn curve to the workpiece using the full size curve of the pair. Similarly, you can layout full size mock ups with the large curves, decide which one looks good, then use the corresponding small curve to incorporate the curved element into your design on paper.

The curves are made from 3mm-thick 3-ply birch. The largest one is 36″ long. The edges are not as smooth as plastic curves, so you might want to do some light touch up with sandpaper using a block to avoid rounding over.
There are tiny holes at corresponding locations in each pair of curves that can be used as reference points to transfer a layout from one curve to the other in the pair. Numbering the holes, as shown here, helps keep track of the paired locations.
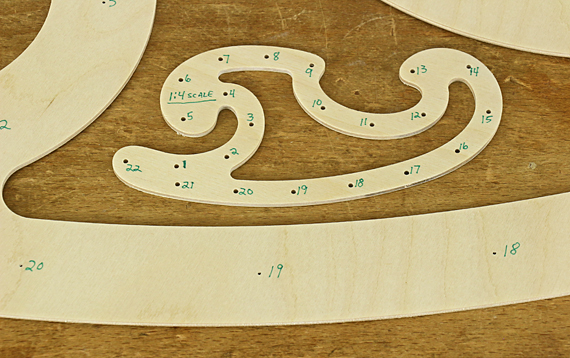
I often use long, very gradual curves in my designs, so I wish Veritas would also produce paired sets like these with very mild curves. I imagine this could be readily done with a CAD-CNC process.
The key to using French curves is to mark the end points of a curve, then “fill in” the curve using at least one (usually two or more) additional reference point(s) to guide the placement of the template. Shift the reference points and use various segments of the French curve until the drawn curve looks the way you want.
Consider using this wonderful rasp for truing curves in templates and workpieces. [If I made a buck from it, I might have called this a shameless plug.]
By the way, why “French” curves? Beats me, but with a little online research, I learned that French curves are based on segments of the Euler spiral, named for the great eighteenth-century Swiss mathematician. The Veritas curves approximate a common Burmester set, named for German physicist-mathematician Ludwig Bermester (1840–1927). So, why aren’t these types of curves called “German curves?”