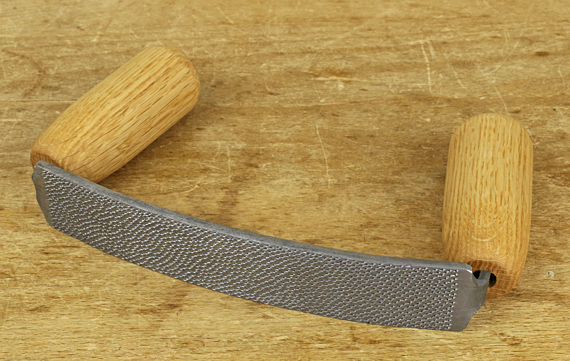
This unique rasp, handmade by Liogier in France, will allow you to deftly produce beautiful curves in your woodwork.
The stitched surface is flat across its 30mm (1 3/16″) width with a shallow convex curve (radius = 320mm) along its 160mm (6 1/4″) length. The robust hardwood handles at each end can be gripped from the sides or over the tops to give you power and control with an in-line push or pull stroke.
You will feel exquisite tactile feedback as you fair gradual curves such as refining bandsawn curves in a table leg or rail prior to final smoothing with a scraper or sandpaper. I suggest grain #10 or 11 for general furniture work.

After years of wishing such a tool existed, I designed this rasp in my shop using wooden and sandpaper mockups, and extrapolating from other rasps. I experimented with various curves, lengths, and widths for the cutting surface, and also put a lot of time into trying different positions and shapes for the handles. I presented the design to Noël Liogier who produced it with his legendary skill. The result: c’est manifique!
It is now available from the Liogier website for €58, currently $66.57.
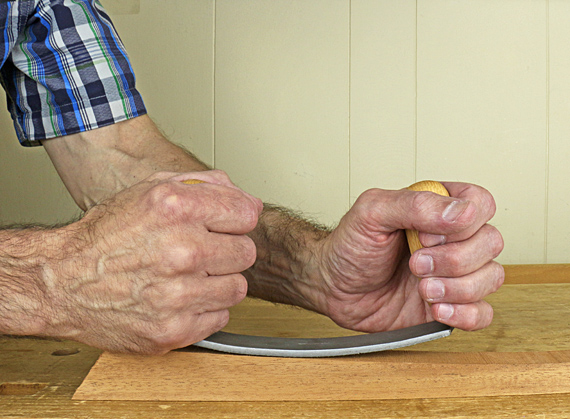
You may find it helpful to visit the post I wrote a few years ago about available options in tools for working curves by hand, and the two posts about the process of fairing curves. There are two key points. First, distinguish between two different processes: shaping the curve and smoothing the surface. Second, when fairing (shaping) the curve, you need a tool that provides continuous tactile feedback of the developing curve. The tool must have sufficient rigidity and length to reduce aberrant bumps and troughs.
This new rasp is far better for fairing curves than other options such as an adjustable float, Surform shaver, or diagonally pushing the convex side of a half-round rasp. It also provides better control and power than do curved ironing rasps for this task. Shorter tools such as a spokeshave or scraper are less reliable for fairing. I also think you will find this rasp more user friendly than a compass plane or other curved-sole planes.
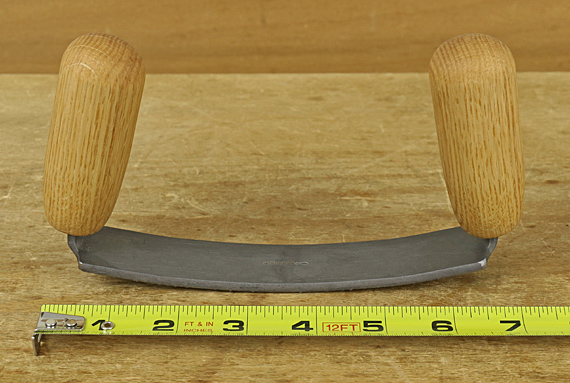
Liogier is one of the two best-in-the-world makers of hand-stitched rasps, both in France; the other is Auriou. This video shows some of the incredible workmanship that goes into these tools. There is nothing quite like using a hand-stitched rasp. This new design adds to the venerable repertoire.
If you do give this new rasp a try, I’d love to hear what you think of it.