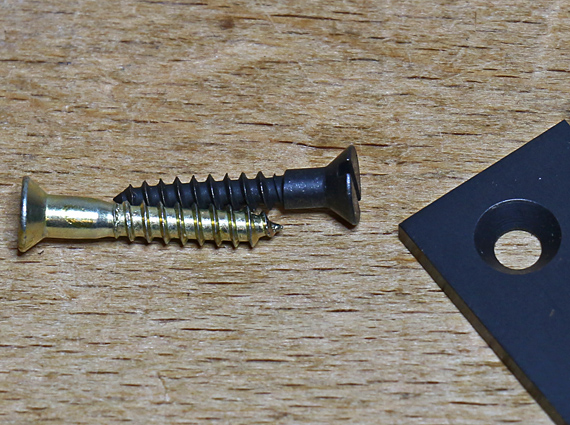
This is just one of those simple little matters that somehow seems to go unattended.
A small solid brass hardware screw, such as a #4, is not very strong and can be easily torqued past its breaking point, leading to all sorts of profanity filling the air of even the most peaceful woodshop. A commonly recommended way to avoid this frustration is to pre-thread the pilot hole with a steel screw, which is stronger.
The steel screw should have the same thread pitch as the brass screw for which it is preparing the way. Otherwise, the preparatory threads will be misplaced and so the brass screw will have to cut most of its own threads anyway. The two sets of misaligned threads may partially merge and probably weaken the wall of the hole in a situation where you want all the holding power you can get.
In the photo above, the steel and (antique finished) solid brass screw threads correspond perfectly. (It is difficult to photograph this in position so please take my word for it.)
Below, the steel screw is a slightly finer pitch and so will cut threads out of sync with the (antique finished) solid brass screw threads. Yes, they are close but that’s just the problem. Not only does this defeat the purpose of the preparatory threading but I think this will also weaken the wood wall and reduce holding power.
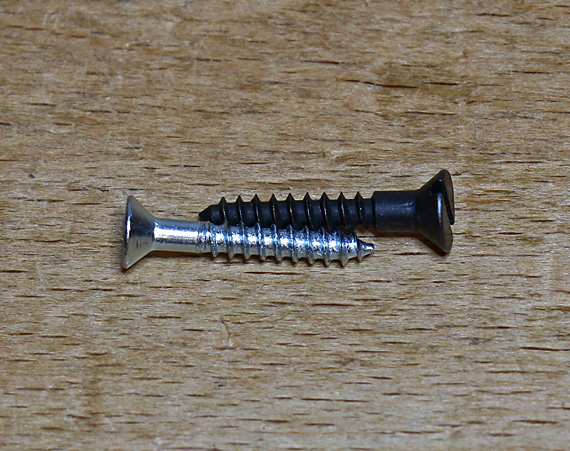
A maker of one the best, if not the best, quality hinges supplies such incorrect steel screws with their brass screws. So, beware and check for yourself.
OK, what if you cannot find a proper steel screw in your Miscellaneous stash? Not a big deal. I find that with proper care, the brass screws hold up well. The key is to first test the screw procedures in scrap wood.
With or without preparatory threading, there is a good chance you will find you have to use a pilot hole that is slightly greater than the root diameter of the brass screw. (The little steel screws can break too!) I also enlarge the upper part of the pilot hole with my Czeck Edge awl to accommodate the unthreaded portion of the screw. It also helps greatly to dab a bit of wax or Slipit into the pilot hole using a sliver of wood (better than on the screw itself) to reduce the torque required to seat the screw. I do not think this reduces holding power.
Part of good craftsmanship is preventing little matters from becoming big headaches.