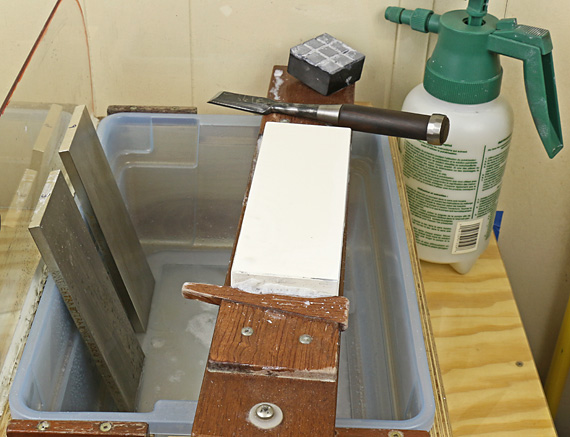
Disclaimer: Or what they do tell you but you might not notice.
Just as you cannot be a good woodworker without understanding a lot about wood, so too, you must be a highly capable sharpener. However, with all the available information and devices devoted to sharpening, it is easy to forget about the other end of the matter – blades get dull.
In fact, a plane blade, for example, starts to dull almost immediately when it is put to work. So, to be practical, you really should think of sharpening and dulling together as a system. Teaching demonstrations may finish with an impressive hair shaving flourish but that is not the full story of what you do in the shop.
The first step in an effective system is to consider the steel type and quality when choosing tools. For example, I value my Japanese chisels for how sharp the edges can be made but more for how long those edges last. The point is to think about how that nice sharp edge is going to play out when you are making things with it.
Here are a few more hints in thinking about a system:
- Each sharpening procedure, including the edge geometry, should be customized to the tool, the steel, and the intended use.
- For smoothing planes and paring chisels, plan your work to make the best use of a pristine edge.
- Consider the trauma incurred in the steel just behind the edge, especially when grinding a fresh bevel. I avoid grinding out to the very edge whenever possible. I refer you to Brent Beach’s site for more on this.
- An edge rarely has to be perfect, and rarely is. Get to work.
- If your sharpening station is not easy to set up, you’ll probably be working with inadequate edges.
Remember that the edge wears on both the beveled and the back (flat) sides. To get a sharp edge, you have to remove the round over on both sides. The back side of a plane blade can be surprisingly prone to neglect when sharpening, even if it was flattened well in preparing the blade when it was new. The solution is David Charlesworth’s “ruler trick.” I use it on almost all of my plane blades.
One more thing: Still not enough attention is given in teaching materials to the need to adjust the amount of camber in plane blades according to the bed angle. I pointed this out more than ten years ago here.
This is the hardest part of getting started with hand tools. Sharpening saws, chisels, planes, scrapers, the list goes on. When it comes to the sharpening station that you have created, you focus primarily on diamond stones, with one MAJOR polisher at the end. Did you move away from your water stones for lack of running water in the shop? Issues with multiple stones being in the same pond water? What drove you away from them?
Now that you have been away and come back to diamonds, do you find your edge has suffered any? Any effect on your sharpening times?
Lots of questions. Always lots of questions about sharpening. Sharpening is expensive. Comparable to hand tools – except on is exceptionally more friable and frustrating.
I used my sharpening station for years before I acquired diamond stones. The spray bottle and the plastic tub obviate the need for running water in the shop. That’s a big advantage of this sharpening station.
I use diamond stones for speed and convenience.
There is no problem with multiple stones at this sharpening station. The plastic tub catches rinse and overspray. None of the stones are at all submerged in water.
Once I started with the DMT DiaSharp stones, I’ve never left them! The sequence that I use efficiently produces excellent edges.
Please see this post: http://www.rpwoodwork.com/blog/2015/09/26/diamond-stones-in-a-sharpening-system/
And this:
http://www.rpwoodwork.com/blog/2015/09/28/suehiro-gokumyo-20000-finishing-stone/
Since then, I’ve added an 8000 Shapton Pro in between the 3 micron DiaSharp and the Gokumyo 20,000, depending on the steel.
Yes, sharpening seems to produce lots of questions. I get more on that subject than any other. No problem – bring ’em on.
Rob
Sharpening is a subject that brings out plenty of comments. Here I am. I have red most of if not all of Brent Beache’s site on sharpening. I always find something to learn and also lead me to question what level of sharpening is really necessary. On the one hand, it seems that it is highly improbable that woodworkers of the past had any way to get a good sharp edge, but we know that isn’t true by looking at the wonderful work that they have done. I personally think that today there is much too much focus on the finer and finer grits, and I am guilty as well. It is as if a plane blade bevel is a facet on a precious jewel.
I think the best advice is to pick a system and stick with it until you gain the experience to achieve the highest level of sharpness of which you are capable. I grew up with oil stones and tried to use water stones for a time, but never got to the point of understanding them at the level of the forms (Plato’s word, not mine.). Then along comes affordable diamond stones and I never looked back. These I would recommend to any new woodworker as the place to start. It is likely to prove a wise investment if ever you think of rehabbing any older tools. Finishing stone is a matter of choice and I have recently returned to using my hard black Arkansas stone, although I have been looking at the Shapton Glass as a possible alternative which will allow me to not mix oil and water in my sharpening system. They are just so darn expensive…. probably equivalent to what I paid for the Arkansas stone 30+ years ago. You see sharpening and the quest for the perfect edge is highly addictive. Now where is that Tormek Catalog?
Daniel, I agree, it is easy to overdo it futzing about with sharpening gear and techniques. I’ve been there and back. That’s why I wrote this post.
Rob
I have read your posts on that polishing stone, I read the post about the Chosera 10K as well. I have read about the diamond stones in your post as well. I love that sharpening station and plan to adapt it to my space.
My main issue right now is working down a system that has expanded to be too much for me. Currently I have the diamond stones you mention as well as the extra extra coarse DMT 8″ stone and the coarse in the same size. I have different polishers; Shapton Pro 5k and 12k, Sigma stones from Japan directly at 6,8,10k and a cheap double sided stone from Amazon that was a long ago input that rarely sees action lol I know there is a lot of overlap in those polishing stones, and no need for those progressive grits. Some of the stones were gifts, some were meant to replace others.
I use my DMT fine, extra fine, and extra extra fine as you do, then head to either my 5 or 6k, then onto either the 8 or 10k and then onto the 12k Shapton Pro. My main issues right now are lapping the stones flat, where or how I would clean the lapped particulate from the lapping plate, and my honing guide.
For the lapping of the stones, I currently use my DMT extra coarse and then follow it up with the DMT fine stone. Do you use your bench stones to lap your Shapton Pro 8K and the GMN 200? Do you not find the diamond plates stick terribly? If not, what do you do to avoid it?
Cleaning the particulate from the lapping plate, you say you manage with that spray bottle. Is that a laboratory type spray bottle? Or a larger gardening type sprayer? I use a spray bottle like you would use for spraying cleaner onto reading glasses. The spray is pitiful, and far too diffuse to use in the wetting of stones, and subsequent rinsing of a loaded diamond stone after lapping. I need an alternative, and something with decent capacity to avoid having to run inside for more water frequently.
When it comes to a honing guide, I’m using an Eclipse-style cheapie. I have tried to follow an article on how to tune it up for better performance, but the bearing is just about shot, the wheel is out of flat, and the jaws now clamp skew. I hollow grind, so learning to hone free hand is up on the docket, but in the interim a DIY honing guide is being put together to take advantage of the stone bridge flat in your design. You just freehand your hollow ground blades, correct?
Thanks for all of the input Rob, it is much appreciated by someone who is very new to the craft, and is young so this information will be carried forward for a good long while :)
Hi RB,
Dude, ya got stones. Actually, as you admit, way too many. Decide on a system and go with it. There is no one right answer. For me, as I described, a succession of diamond stones followed by one or two fine ceramic stones does the job.
That is an old photo (I was too lazy to take a current photo) but I now use a better spray bottle: Flomaster 56HD https://www.homedepot.com/p/RL-Flo-Master-4-pt-Hand-Sprayer-56HD/100164531
The sharpening station is not hard to build and I still recommend it.
I find have to flatten the ceramic stones infrequently. I refresh the surface very often with my “diamond naguras,” one each for the Gokumyo and the Shapton Pro. See my posts on diamond naguras. I use homemade versions but decent substitutes are available from Chef Knives To Go online.
I still use my old Shapton diamond lapping plate on the ceramic stones but it is wearing out. I think I’d try one of the NanoHone plates made by Hap Stanley:
https://nanohone.com/collections/lapping-plates
Regrading honing guides, I’ve got some posts on a low tech, partly hand method, and also the Veritas with a shopmade accessory.
Good luck.
Rob
Lol I do have stones. I agree completely, I need to whittle it down to the stones that do what need to be done, and get me back to work. I, like you, prefer the diamonds for the majority of the process. I would like to nail it down to 2 polishers like you as well. One day the GMN-200 will sit in my pond lol.
I am without a doubt building your sharpening station, as well as your router table (more questions to come on that on different posts). I will pick up a spray bottle like that. I can see with a spray bottle with a literal stream from the outlet, being able to get by without running water. I think I am lapping my stones too frequently. I have the Shapton Pro stones, I think lapping them after 3 blades, with microbevels, is exccessive. I am going to build a few of your homemade diamond naguras. Seems like a good idea. I have a plastics guy nearby that is a friend of mine, I’m sure there are offcuts that can come my way.
I would be keen on a NanoHone, I have Atoma diamond plates on my Christmas list. Lets see if Santa is good to me. I will try to look for your honing guide posts. There is some very handy information on here, but it is a mix of skill/experience with the intent that makes it tricky to implement sometimes – example; your post on using a straight edge, and the “pivot” technique for checking lumber. Tried it, was terrible at it. I think the issue was finding specifically where wood needed to be taken off when I actually brought a plane to the wood surface. I digress. Thank you for the responses. I appreciate it very much!