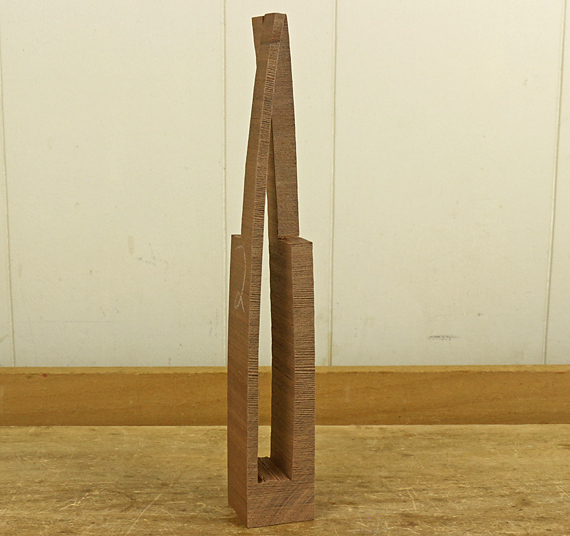
Other posts here have addressed the issues of case hardening, its effect on resawing, and the problem of excessive case hardening. But here’s a new twist.
To review, slight case hardening is to be expected in kiln-dried hardwoods. Here’s a simplified explanation of what happens in the kiln. Think of the board in cross section. The outer shell loses moisture first, making it want to shrink but it is restrained by the still moist and swollen core. The shell is thus in tension and the core in compression. The shell eventually sets in size, so later when the core loses moisture and wants to shrink, it is in tension while the shell is in compression. This is case hardening.
The kiln operator modifies the humidity near the end of the process to remove most of the case hardening but is careful not to go too far and create reverse case hardening, which is not practically correctable. Therefore, there is a bit of remaining case hardening in most kiln dried hardwood boards. It is not normally a problem.
Excessive case hardening, usually from inadequate air drying before going to the kiln or rushing the wood through the kiln, is a problem. This manifests most notably if the board is resawn. Both halves will cup inward toward the sawn surface and may bow inward a bit along the length. We can predict this with a test fork.
It is important to appreciate that this is not a matter of a remaining moisture content gradient across the thickness of the board! It is a physical stress caused by the drying process that releases when it can, which is typically right away or very soon after resawing or removing substantial thickness from one side of the board.
But how long can it take for the release of tension and consequent distortion of the board to fully manifest? From everything I have experienced (and read), it is mostly almost immediate, or in some cases it can trickle on for a day or so.
But this case is different.
I recently resawed some 8/4 quartersawn sapele. The boards were straight and true with nice, even straight grain. There was absolutely no moisture gradient across the thickness of the boards, as proven with pin meter readings at various depths across the end grain of fresh crosscuts well into the length of the board.
Test forks looked great – little or no inward bend of the tines – so I did the resaw. But after a couple of days, I was shocked to see the tines hooked inward. (The photo above is how they ended up.) The boards themselves distorted over several days. They showed both the classic effects of case hardening, and more disturbingly, some twist. I hate twist.
The wood seemed to settle down after a couple of weeks, so I dressed the resawn boards but then even several weeks later I could still find a small but significant amount of new distortion, primarily twist! Again, the grain of the boards was nice and straight. Furthermore, they contained no evidence of reaction wood, or other aberrations. The resawn wood was stored stickered and at a steady 50-55% relative humidity.
Why did it take so long for the distortion to fully manifest? I don’t know. Some online research and talking with experienced log millers, though hardly exhaustive, yielded no answers.
Here’s my little theory. For the mechanical release of tension (that creates the distortion) to occur, I assume the wood fibers have to slide against each other. Perhaps that sliding is just “stickier” and slower to occur in sapele than in most woods. Perhaps related, I note that sapele is among the highest measured woods in shear strength (at 12% moisture content) listed by the U.S. Forest Products Laboratory. (Wood technologists and scientists, please comment!)
In any case, it happened. Wood stresses can be stressful. So, there it is, one more caution to take with wood.
Rob, your theory is a good one and I agree with it to some extent. The high strength internal structure of Sapele plus its heavily interlocked grain means that is can withstand a lot of stress. Also African woods and most tropical woods contain a much higher extractive content which acts to ameliorate the moisture changes and leaves the wood more pliable. But eventually that strength gives out without support and actually unravels. The interlocking grain un-spirals and that lead to the twist.
What I suspect is that just the shop climate conditions, even if climate controlled, fluctuated a bit and over time that worked to be the catalyst for deformation. In other words, a little bit of moisture infused into the fibers, then dumped, then infused, then dumped, etc. This acts like bending a credit card back and forth until the plastic weakens and then finally snaps.
Around the lumber yard where I work, Sapele is one of the most common species we stock. It is reknown for remaining super stable after milling but in instances where precision is asks for (like with T&G porch flooring or siding) we will assemble the joints before packaging and shipping because over the course of a week the size of the groove will change. This isn’t just Sapele that exhibits this behavior but several other African species and some South American species where interlocked grain is common and oil and resin content is also high.
Wow, Shannon, great explanation!
OK, so sapele’s high shear strength, high resin and extractive content, and interlocked grain act to create this “slow release” of internal stress. Small fluctuations in moisture content also “loosen” the wood fibers to release the stress.
Thanks for this insight. Once again, knowledgeably watching the wood is so important to woodworking.
Rob
May be way off-base here but it may be because of how this was cut. When you cut the piece from the center down toward the bottom, it leaves the two arms with concentric tree rings going down the length of the board that will curve toward the the center of the tree (assumes riven). It is further exaggerated by the releaf cuts half way up the board allowing a even faster bow/twist to occur. Now the bottom is fixed in place and can’t move. This may well be a result of the mechanical stresses in the wood itself releasing in the direction of spiral left when the center was removed. Of course this is all conjecture because I can’t see any of the grain from the picture.
No problem, Antony, but let me clarify. The piece of wood in the photo is a test fork taken from an end cut. The middle is cut out to test for internal stress in the board, especially looking for excessive case hardening, which this board certainly has.
The question here is why there was the delayed, gradual manifestation of the internal stress (from excessive case hardening) after resawing the 8/4 board into two boards. It is usually shows up just about immediately.
But I think Shannon has given us a good explanation.
Rob
Hi, great posts of late. I completely agree on all your points! A boon of info for the uninitiated. My ONLY suggestion might be to change “case hardening” to the correct term, “Tension Set”
Thanks, Corey.
“Case hardening” is in fact the term found for the condition I describe here in the U.S Forest Products Laboratory’s Wood Handbook and in the late Professor Bruce Hoadley’s seminal book, Understanding Wood, and generally elsewhere.
Rob