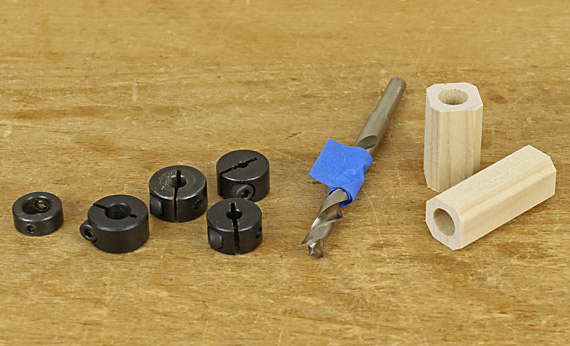
Maybe.
Of course, the best drill stop is on a drill press but the topic here is drill stops for hand drilling, which for most of us means with a portable electric drill, corded or cordless. So, let’s look at the candidates.
The most common store bought drill stop is a round metal collar with a single setscrew that tightens against the drill bit. These are cheap and not bad, but I’d stop short of calling them good. Most of them tend to tilt as the screw is tightened and all of them can damage the flutes of the bit. If you jiggle or turn the collar to direct the point of the setscrew toward the bottom of a flute and then tighten the screw carefully and firmly, they can stay put and perform decently. Fuller makes a version of these that is longer than the others.
Another type of stop uses a setscrew to close the metal collar’s diameter to bind it by friction against the drill bit. I’ve found that the metal is too stiff to reliably close down snugly against the bit, or on the other hand, that the inside diameter is too close to that of the drill bit so the collar is too hard to get on or off the bit. They’re borderline acceptable; I wouldn’t call them good.
Some of the stops used in conjunction with a countersink are pretty good and some of the Forstner bit stops seem good but those are other matters.
An utter failure is the red plastic stop that twists on and supposedly tightens against the drill bit. I have found them totally unreliable – they easily slip. Sorry, I wouldn’t use them in a hundred years on any project of importance.
Now let’s look at what I think most of us use: masking tape. Wrap some blue tape tightly around the drill bit and squish it in against the flutes. Then fold over the last bit of length so it forms a little flag that sweeps away the drilling dust on the work piece to signal that you are at full depth, and later to make the tape easier to remove.
In any careful work, I put a mark on the drill bit at the bottom of the tape with a Sharpie. Then, as I’m drilling successive holes, I check repeatedly to see if there is a gap between the mark and the tape, which would indicate that the tape has slipped. Alternatively, I keep checking with a ruler.
What about for very careful work, especially drilling many holes, such as in carcase dowelling? For this, remove all doubt and make a dedicated wooden collar drill stop as James Krenov recommended.
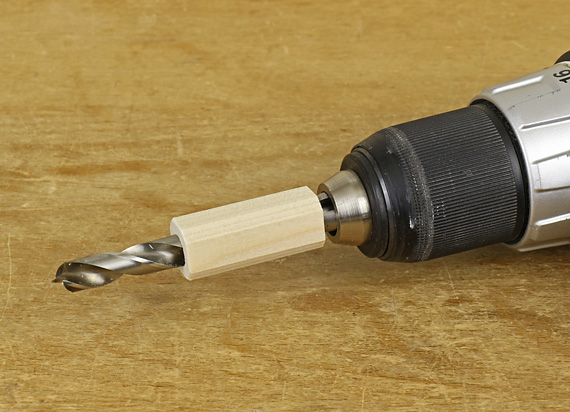
Work out the required length according to the desired depth of the hole and the length of the drill bit. Use a drill press to bore into the end grain of an over-wide squared block then saw off the stop itself. Chamfer the long corners for safety so they won’t hack at your fingers. If you cut the cross section of the stop to size before drilling, it will register less accurately against the drill press table and the drilling is likely to be dangerous.
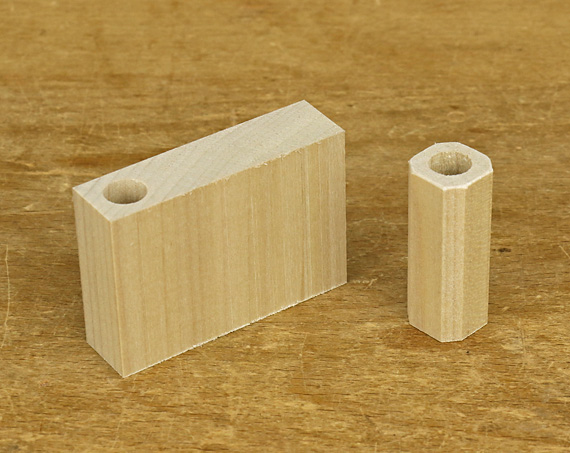
The cutting depth can be fine tuned by adjusting the amount of the drill shank inside the chuck – assuming it is a good chuck. This type of drill stop has never let me down. It’s worth the extra effort. By the way, dentists understand this.
So, yes, there is a good drill stop, but you have to make it.