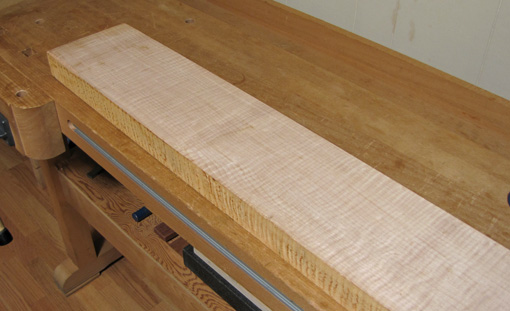
Look at the lovely curly maple above. #%$@! sticker stains – the shadowy bands of discoloration across the width of the board. They are seen at the regular spacing where stickers are placed in a stack of boards prepared for drying.
Whatever their cause, perhaps wet stickers and/or slow drying, they are common only in light species, especially soft maples, in my experience. The stains are not usually visible on the rough-sawn surface, but only after planing, and even then they may go unnoticed until the board is viewed from several feet away. The discoloration can penetrate surprisingly deep. Fortunately, in this board the discoloration is shallow and there is thickness to spare.
As evil as it gets, is honeycomb. I do not have a photo to share because I cannot stand keeping such wood in the shop. These are splits oriented along the rays in the core of the wood that reveal their hideous grin on the end grain after a board is crosscut. Honeycomb is basically an extreme form of case hardening caused by poor drying, usually in thick wood. I once brought a gorgeous 8/4 curly koa billet into the shop only to have my thrill doused to disappointment after crosscuting revealed extensive honeycomb.
Even common end checks can be tricky. Sometimes these can partly close, hiding the compromised wood that extends further than the open check into the length of the board. To be assured of using only sound wood, mark the location of a sizeable end check, then saw 1/4″ slices from the end of the board and observe where they break. When the slices are taken in sound wood, they can be snapped to break randomly, not at the location of the end check.
The two boards of curly red oak, below, are parts of batches that I bought at different times. They are both nice but the colors do not match. I will have to use them in different pieces or at least for different categories of parts in one piece.
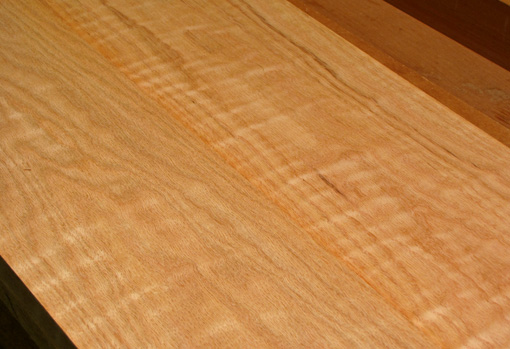
In a perfect world, we could obtain all the wood of a species in a project at the same time from a single tree. The boards would be hit-or-miss planed to preserve thickness, reveal most defects, and allow for good color and figure matching. Skim planing and keeping boards organized by flitch are more work for wood dealers and add to cost, so, while available, they are not usual practices.
When new wood comes into the shop, I give it another once-over and then write on each board the date and moisture content as measured with a Wagner pinless meter. The boards get stored so air can circulate all around them. If the wood has particularly high moisture, is very thick, or is otherwise prone to end checking, I coat the ends with a wax emulsion such as Anchorseal 2. I then observe the wood for a few days to a few weeks, depending on the species, thickness, and initial MC, rechecking until the MC levels off.
When planning the parts for a project I think carefully before major crosscuts because those are usually big commitments. For thick stock, such as 8/4, I use a pin meter to check for any moisture gradient across the fresh crosscut.
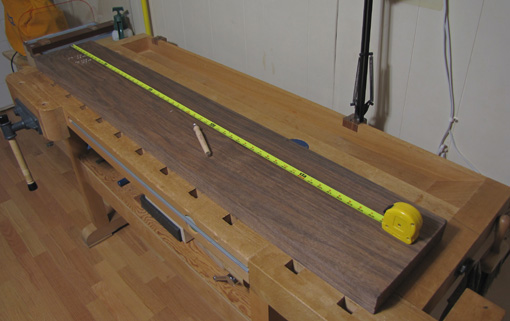
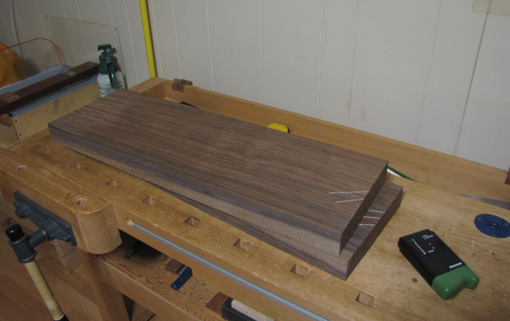
So, while wood disappointments do come along, wood elations are much more frequent and they last a lot longer!